Specialists training
Report on the results of the study tour conducted on October 24-28, 2005, to train a group of specialists from the Republic of Belarus in power engineering, energy efficiency, and forest industrial
production under the UNDP/GEF Project entitled "Biomass Energy for Heating and Hot Water Supply in Belarus"
The study tour objective was to train the Belarusian specialists in various aspects of harvesting, transporting, storing, and using wood fuel at power plants on the basis of experience gained in Finland and other European countries.
The training course was attended by 9 energy sector and forest industry specialists who are currently engaged in designing technologies and machinery systems to be used in the production of wood fuel, selecting power plants capable of efficiently burning wood fuels, and organising the production and operation of wood fuel-fired power generation systems.
The training programme was implemented in 5 working days – from Monday 24/10/05 to Friday 28/10/05.
The city of Joensuu – the administrative centre of the north-eastern province of North Karelia, which is the most developed region of Finland in terms of wood harvesting, wood working, forest research, manufacturing up-to-date forest machinery designed for various applications, introducing on a wide scale the progressive methods for producing, transporting, supplying, and using wood fuels at the existing power plants of various capacities, was selected as the basic training venue. The Finnish institutions and enterprises that participated in implementing the training programme, designed for the Belarusian specialists, included: Puuteknologiakeskus, the Research Institute of Wood Processing Technology (the abbreviated name – PUUGIA), the Finnish Forest Research Institute in Joensuu (with the headquarters in Helsinki, the abbreviated name – METLA), the Joensuu University, the well-known manufacturers of forest harvesting machines and equipment including John Deere Forestry, Timberjack, Kesla, Pentin Paja, the companies specializing in wood harvesting and fuel chip production, and power plants (cogeneration plants) of various capacities located within the distance of 100 kilometres from the city of Joensuu.
In accordance with the programme prepared and agreed with the Finnish party, the theoretical training and practical studies were held on the PUUGIA's premises with the participation of professors and scientific workers invited from the above-mentioned research institutes and the university (usually in the first part of the day), and the study or detailed familiarization with the production processes, machinery and equipment in the course of work (in the forest, at co-generation plants) or the machinery or equipment manufacturing processes (at manufacturing plants) were conducted by visiting the respective sites and facilities in the second part of the day. An interpreter versed in the Finnish, English and Russian languages and the training administrator appointed by the Finnish party were constantly present at all training sessions to assist in achieving maximum understanding and assimilation of the training material and the related information.
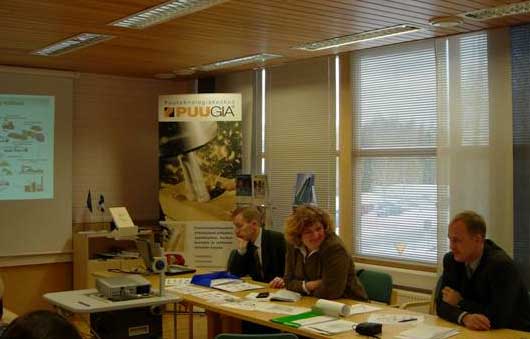
Fig.1. The room in the PUUGIA's administrative building used to conduct the training sessions.
Finland is the world leader in the utilization of biomass for energy purposes. Finland attaches much more importance to the generation of energy from wood fuels than other industrialized countries as it does not have its own deposits of oil, gas, coal or other fossil fuels (except for peat deposits). At present the share of energy produced from wood fuel constitutes 20% of the country's fuel balance.
In Finland forests occupy the total area of about 20 million ha covering about 2/3 of the land territory of the country. 53% of the forests belong to private owners, 34% to the state, 8% to companies. The main forest forming species are pine (47%), spruce (34%), birch (34%), aspen and other species (5%).
The annual wood harvesting volume amounts to 77 million m³ including the consumption of wood as a raw material for mechanical processing (bolt timber, veneer logs etc.) – 32 million m³; and for chemical and chemical/mechanical processing – 38.5 million m³. Although a high percentage of timber is processed to manufacture timber products (78%), about a half of the total harvested roundwood volume is ultimately used as fuel. At present in Finland the approximate annual consumption of wood raw material used to produce energy constitutes (fuel-wise): lignin – 17.5 million m3 (on solid mass basis), bark – 8.5 million m3, firewood – 5.8 million m3, sawdust – 3 million m3, fuel chips produced from logging residues – 3 million m3 (2004), the production forecast for 2010 – 5 million m3.
In 2004, in Finland there were 485 chip-fired boiler plants and co-generation plants with capacities exceeding 0.4 MW.
The relative share of various fuels in the country's energy balance is as follows: oil – 27 %, wood – 20 %, nuclear fuel – 17 %, coal – 12%, natural gas – 11 %, peat – 6 %, hydraulic power stations – 3 %, other fuels – 1 %, imported electric power – 3 %.
In 2002, the percentage of wood as compared to other fuels used in the European Union countries for the production of energy was: 20,8% in Finland; 14,0% in Sweden; 5,65 in Austria; 5,5% in Portugal; 4,5% in France; 3,3% in Greece; 2,9% in Spain; 2,4% in Switzerland; 1,9% in Germany.
The above few quantitative indicators, although not aiming to constitute exhaustive information, confirm the correctness of choice of Finland as a place for training and the object of study with respect to the technology and methods of production and supply of wood fuel to power generation enterprises.
The summary of the main training course topics, the demonstration of the equipment and technological operations relating to the topics under study, and the results of the visits to the main firms and institutions working in the field under consideration are described below.
Although wood biomass as an energy source (Prof. Pavo Pelkonen, the Joensuu University) has a lower calorific value as compared to fossil fuels, it also has a number of important advantages. The main advantages include the renewable nature of wood fuel, the lower carbon emission from the fuel being burnt, a much lower concentration of hazardous substances in ash as compared to mineral fuels and coal and peat, the possibility to grow and harvest the fuel close to the consumption facilities decreasing by many times the distance of transportation from the place of origin to the place of consumption etc. In many countries it is the local fuel that can save the money used to buy the imported fuels.
If the total tree biomass is taken to be 100%, the stemwood, traditionally used as a raw material for processing wood to produce various wood materials, constitutes only 60-65% and the limbs, the branches, the top, and the foliage (the crown) – 20-25% of the total biomass volume; the remaining volume includes the stump and the roots. If the harvested volume is considered to consist of stemwood alone by taking it to be 100% (which is a common practice in the CIS countries including the Republic of Belarus) the harvesting process produces in addition to commercial wood 30-45% of felling debris in the form of the cut crown on the ground and 20-25% of the root biomass underground. The part of the tree biomass comprised of the crown, the stump, and the roots, which quantitatively constitutes about a half of the volume of the tree stemwood (commercial wood), may be used as an additional raw material in the production of energy.
At present in the countries of North America, Europe, Scandinavia, the Baltic Sea region, and the CIS (including Russia and the Republic of Belarus) the industrial harvesting operations are performed using three essentially different logging methods (Prof. Antti Asikainen, the Finnish Forest Research Institute (METLA)):
1 – a method for harvesting assortments at the stump area and transporting the harvested timber to a customer or to an industrial log depot by short log trucks (the cut-to-length or CTL method);
2 – a method for harvesting tree lengths in the logging area and transporting the timber in the form of tree lengths (a tree length is the entire delimbed tree stem) to an industrial log depot for further processing (the tree-length or TL method);
3 – a method for harvesting full trees in the logging area and transporting the timber in the form of full trees by timber trucks used in the method described in i. 2 to an industrial log depot for further processing including delimbing and bucking the trees, sorting and piling the roundwood sections, etc. (the full-tree or FT method).
Respectively, these methods will determine both the characteristics and selection of the machines to be used to produce fuel chips from logging residues and low-grade wood and the production volumes of chips as the volume of the raw materials to be processed into chips will depend on the method used to harvest wood.
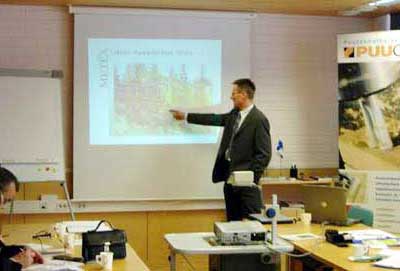
Fig. 2. Professor Antti Asikainen from the Finnish Forest Research Institute (METLA) reading a lecture.
Fuel chips can be produced from logging residues and small-diameter wood both from the final and intermediate harvesting operations using three different production processes implemented at various stages of the wood harvesting system:
- option A is used to produce fuel chips by comminuting the raw material directly in the logging area within the machine trail (strip road), at the loading point (forest timber storage area), or on both sites (the terrain chipping method);
- option B is used to comminute the logging residues and small-diameter wood from the thinning operations accumulated at a special temporary storage area (landing) located on the side of a year round road by mobile chipping machines following the natural drying of the piled wood to the required level of moisture content (the chipping on road side method);
- option B is used to comminute the wood raw material delivered to the terminal, which in Finland is usually the fuel preparation area of a large co-generation pant using wood fuel (the chipping at power plant method).
In options A and B and, in some cases, in option C the first main operation used to collect and transport the wood material to be processed into chips is performed using a load-haul-dump machine (a forwarder). The final logging and early thinning operations carried out in small-size cutting areas usually located in the forests belonging to private owners can be effectively performed using conventional wheeled tractors with trailers and cranes (see Fig. 3).
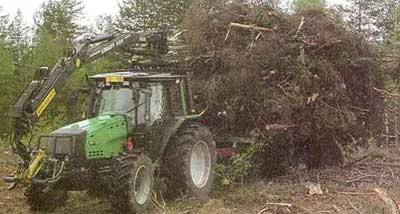
Fig. 3. Transporting logging residues to the comminution or storage area for further processing to produce fuel chips.
The experienced tractor operators using high-capacity cranes place the delivered wood material in piles up to 6 m high and from 40 to 50 m long using the piling method ensuring the maximum protection of the piled wood material from being moistened by atmospheric precipitations (see Fig. 4). Such piles formed at roadside landings (according to the wood harvesting terminology used in Belarus, "in intermediate storage areas") from various types of wood are stored for a certain period of time before being comminuted into fuel chips using drum chippers with upper discharge capable of loading chips directly into chip trucks (see Fig. 5) that deliver the chips to a boiler plant or a cogeneration plant.
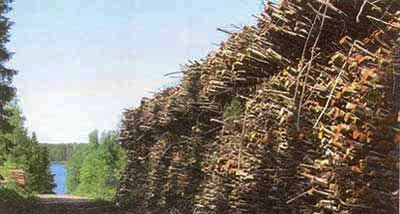
Fig. 4. A pile of small-diameter tree-lengths delivered after performing the thinning operations and piled at the roadside landing for drying and subsequent processing into chips using drum chippers (one can clearly see that the upper pile layer is formed using longer tree lengths to protect the lower pile layers from atmospheric precipitations).
It should be noted that in Finland drum mobile chippers are usually used to comminute timber and timber residues into fuel chips according to options A and B. There are three common design solutions used to operate drum chippers in combination with driving and hauling mechanisms:
- mounting a chipper on a tractor-towed trailer with a pneumatic undercarriage; in this case, the trailer is additionally equipped with a hydraulic crane used to feed the wood raw material and the chipper cutting mechanism (see Fig. 5), the feeding crane drive hydraulic system and other equipment; all mechanisms mounted on the trailer are power-driven by the tractor engine via the cardan shaft. The tractor ensures the mobility of the unit over the transportation routes;
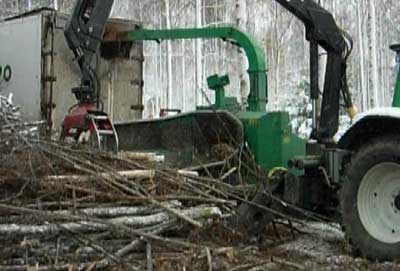
Fig. 5. Chipping the small-diameter tree-lengths collected from piles using the Foresteri – Ñ4560 chipping machine driven by a 200 h.p. tractor engine to produce chips loaded directly into the chip truck.
- mounting a chipper on a trailer in combination with a self-contained driving engine (usually a 150-300 kW diesel engine) and a hydraulic crane with the control panel installed in the cabin of the hauling tractor that is designed only for on road use. This option ensures higher productivity than the previous option and easily fits into the chip production process used at a boiler plant or a cogeneration plant (in the RB, at the harvesting enterprise timber depot or a boiler house timber depot) as its design is close to a semi-stationary option, and the diesel engine may be replaced by an electric engine;
- mounting a chipper on a chip truck (usually between the driver's cabin and the chip container) in combination with a hydraulic crane, which provides the chip producer/supplier with a multipurpose machine capable of performing all principal operations (Fig. 6). The machine can be effectively used to serve the scattered small-size logging areas with short transportation distances from the logging areas to chip consumers.
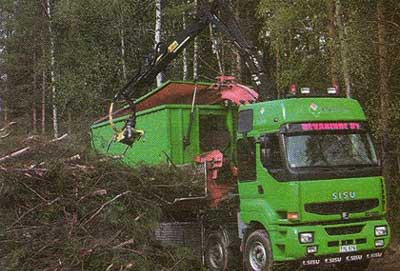
Fig. 6. A chip truck equipped with a chipper and a hydraulic crane.
The production of fuel chips using option C (comminution of wood at a CP fuel depot using high-capacity chippers) is not a wide-spread practice in Finland. Suffice it to say that out of 485 wood fired boiler and cogeneration plants and only 6 plants use stationary chippers. The cost of investment required to procure high-capacity chippers used at such sites is 1-2 million euro. However the main obstacle for developing this option is a low bulk density of logging residues as compared to forest chips (the difference is two- or three-fold) causing high transportation costs. According to experts, the solution of this problem may be facilitated by including in the wood raw material preparation process a residue baler that compresses and ties loose residues (mainly logging residues) into compact easily transportable and chippable bales with the transportation costs per solid m³ of residue bales not greater than the transportation costs per solid m³ of chips or even logs. The respective research has been conducted and the research results are being introduced into production: John Deere has already manufactured 30 Timberjack 1490D residue balers (see Fig. 7) including 20 machines that are currently used in Finland.
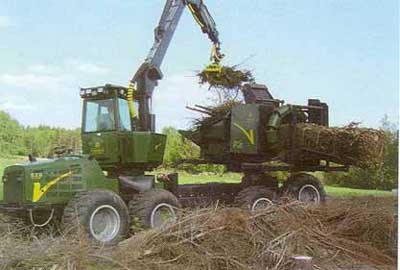
Fig. 7. Timberjack 1490D residue baler at work.
The machine shown in the figure forms and ties the bales 700-800 mm in diameter and 3.1-3.2 m long at the rate of 1-30 bales per hour depending on the type of the raw material and the operating conditions. Following the delivery the bales can be placed in an ordered pile for drying that are stored before being chipped in the intermediate storage area (see Fig. 8) or at a boiling or cogeneration plant timber depot.
The calculations have shown that more than 20 residue balers being currently used in Finland to produce fuel chips could tie into bales almost a half of all logging residues produced in the country.
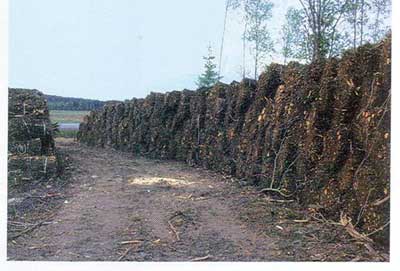
Fig. 8. The piles of compressed logging residues formed in the intermediate storage area (at the roadside landing).
In the course of training, in accordance with the agreed programme the Belarusian group visited and inspected a number of power generating enterprises of various production capacities using the comminuted wood as a fuel. When visiting these facilities the group focused on studying in detail the shops receiving, evaluating, and unloading the wood fuel, the wood fuel storage systems, the methods for composing the optimum mixtures of various types of fuels before feeding the wood fuel mix into the boiler furnace, and the wood fuel feeding systems.
The first facility visited under the above programme was the 200 MW E-ON cogeneration plant owned by a German-Finnish firm that supplies heat and electric power to Finnish consumers. Under full load the cogeneration plant burns 2000 m³ of fuel chips per 24 hours: accordingly, its fuel shop is capable of receiving the chips, testing the chip samples in the laboratory, treating the unloaded chips according to the prescribed method, and feeding the treated chips into the boiler furnace. About 50 chip trucks arrive and unload the chips at the cogeneration plant every 24 hours. Fig. 9 shows the general view of the cogeneration plant main building, and Fig. 10 shows the chips storage area.
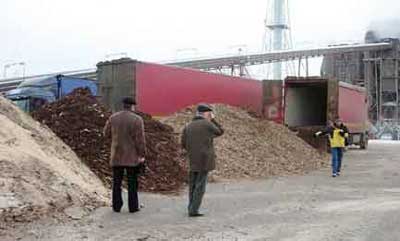
Fig. 9 (above) and Fig. 10 (below).
Apart from the impressive compactness of this high-capacity (200 MW) cogeneration plant, its high engineering and production standards, one should also make note of the following features of the plant fuel supply system:
- the maximum amount of wood fuel in storage does not exceed the 24-hour consumption volume – the continuous operation of the CP is maintained due to the regular delivery of fuel chips by fuel suppliers in accordance with the delivery schedule;
- there are no outdoor fuel chip storages, which ensures the constant moisture content of fuel and improves the ecological conditions and production standards;
- the storage facilities are designed to receive various types of fuels (peat) that are mixed before being fed into the furnace in the required proportions to ensure the required combustion conditions.
Fig. 11 shows the main storage tanks (bunkers) containing the stock of fuel (chips and peat) sufficient to maintain the continuous operation of the CP for the period of at least 24 hours.
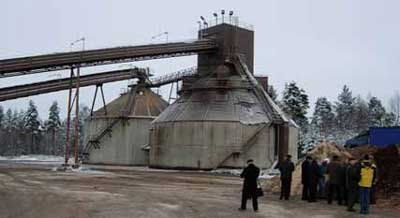
Fig. 11. The bunkers used to store fuel at the E-ON cogeneration plant.
The next power generating facility visited by the group was the 0,6 MW boiler plant, operated by the Tupovar energy cooperative, shown in Figs 12 and 13 with Fig. 12 showing the part of the facility containing the boiler and Fig. 13 showing the opposite side containing the fuel chip closed storage with a platform used for unloading chip trucks and the equipment designed to receive, store, mix, and feed the fuel into the boiler furnace.
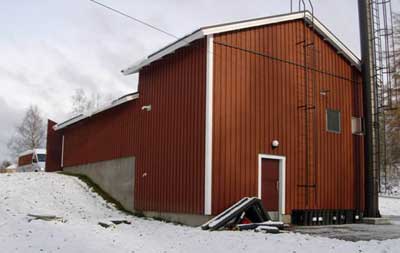
Fig. 12. The general view of the 0,6 MW boiler plant operated by the Tupovar energy cooperative showing the high part of the building containing the boiler (the house is designed and built using the terrain fold: the lower part of the building contains the platforms used to unload chip trucks, and the fuel chip storage with bunkers; the equipment designed to mix various fuels and feed the wood fuel mix into the furnace is located on the high side).
The mini-cogeneration plant adjoining the settlement supplies heat and hot water to the multi-storeyed residential louses, the shops, the hospital, the public and amenity buildings, and some individual private dwellings.
The Tupovar energy cooperative has the second boiler plant located at the distance of 0.6 km from this more loaded boiler plant. At present the works are carried out to form a single heat-supply system so as to level the loads handled by 2 boiler plants.
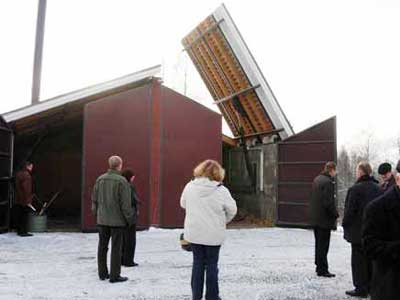
Fig. 13. The boiler plant operated by the Tupovar energy cooperative showing the part of the building containing the fuel storage (with the gate opened and both roof sections lifted by the hydraulic system, two chip trucks can be unloaded simultaneously by dumping the fuel cargo backwards).
According to the programme, the familiarization visits also included a visit to the 10 MW boiler plant operated by Ottocumpu Energia that is classified as a medium capacity power plant. The boiler plant burns the chips produced from logging residues, bark, sawdust, and partially peat. A large reserve stock of chips produced from low-grade wood is placed for storage for the winter period at an open area specially allotted for this purpose.
The general view of the main boiler plant building is shown in Fig. 14.
This boiler plant differs from the previous two power plants in that it has an open fuel storage area used to store fuel chips, sawdust, bark, peat, etc.
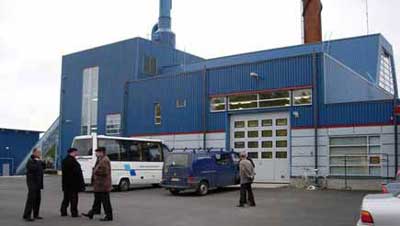
Fig. 14. The general view of the main building of the 10 MW boiler plant used by Ottocumpu Energia.
Fig. 15 is the general view of the outdoor storage designed for storing loose fuels consisting mostly of the comminuted logging residues. At the background on the right-hand side one can see a high chip pile covered by a film material to protect it from atmospheric precipitations. Depending on climatic and weather conditions as well as the condition of the chips inside the pile, the film cover may be partially or completely removed (see the photograph).
The outdoor fuel storage is located at some distance (20-100 m) from the receiving bins installed under the roof (see Fig 16) where, if there is a sufficient free space, 3 chip trucks may be unloaded simultaneously (there are 3 fuel-receiving bins installed under the roof below the ground level; each bin has a capacity of 150 m³ making the total capacity of the indoor storage section 600 m³). If there are no chip trucks delivering fuel chips or it is necessary to mix various types of fuels, a payloader is used to deliver the chips from the outdoor chip piles to the bins.
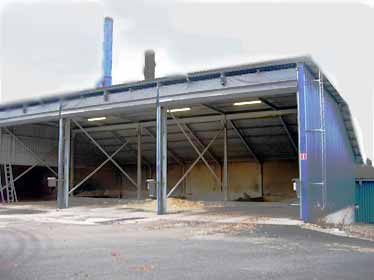
Fig. 15 (above) and Fig. 16 (below).
It became clear in the course of training and during the familiarization visits to the wood harvesting and power generating enterprises that Finland does not face the problem of neutralizing, utilising, or burying ash formed by burning wood fuels and peat. Ash is applied as fertilizer to the forest soil in the amount of up to 4 tons per 1 ha using the machines specially designed for this purpose (see Fig. 17).
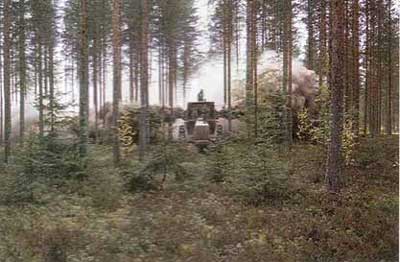
Fig. 17. The machine, designed for spreading the ash formed by burning wood fuel, is moving along the machine trail.
In windless weather, the machine shown in Fig. 17 spreads ash within the strip 20 to 25 metres wide. As the machine trails are usually made every 20 m, the machine ensures a uniform distribution of ash over the entire forest area.
In the course of training and during the meetings with the Finnish specialists engaged in harvesting, comminuting, and transporting wood fuel, much attention was paid to the formation of prices and cost of wood chips.
It should be noted that in Finland this issue has been given special attention. The system of highly efficient and productive machines being currently used in the country to harvest, remove, process and transport logging residues to boiler and cogeneration plants was established in accordance with decision made by the Government with a view to decreasing the price of fuel chips and maintaining it at the level of not more than ˆ7 per 1 MWh (0,86 Gcal), and creating a wood fuel market where at present there are several large highly-efficient operators working at a minimum level of profitability. It is important to note that this objective was achieved and the wood fuel price was constant in Finland over the period of 10 years remaining at the level of $6 to $8 per 1 MWh (all payments involving wood fuel are made using the energy equivalent rather than the volumetric or weight units).
Over the last two years the cost of fuel chips has increased in Finland and is now ˆ10.4 per 1 MWh on the average (which is equivalent to $101.6 per TOE). This increase was caused, primarily, by granting the boiler and cogeneration plants the right to trade in CO2 quotas. According to the information provided by the Finnish experts, 1 ton of burnt wood used to substitute fossil fuel reduces the amount of greenhouse gases by 1-2 tons. The cost of 1 ton of carbon dioxide at the Finnish market is ˆ20-22. Thus each wood fuel ton brings the additional profit of ˆ24-26. The additional profit obtained by the owners of boiler and cogeneration plants from burning wood fuel has allowed the wood fuel market operators to raise the wood fuel prices, although these prices has been also affected by other factors such as the growing oil and gas prices at the world markets and an increase in demand for wood fuel.
It should be noted that despite the minimum level of profitability the production of fuel from logging residues is economically efficient and is not subsidized by the state. The exception are the logging residues from sanitary fellings and forest cleaning operations. In this case, due to the high labour intensity of the harvesting operations, the chip production cost reaches ˆ14-16 per 1 MWh. In this case, the difference between the production cost and the market price is subsidized by the state. These subsidies are included annually in the state budget.
The structure and magnitude of expenses of the fuel chip cost are presented in the figure below.
As the cost of natural gas in Finland is about $180 per 1000 m³, it is economically profitable to use wood fuel. Wood fuel (in the energy equivalent) is 1.5 times cheaper than natural gas.
The preliminary estimate of the cost of the fuel chips produced at final fellings and thinnings in Belarus, partially using the Finnish technology with a lower degree of mechanization and larger share of manual labour, shows that the cost of the fuel chips delivered to a boiler plant over the distance of 50 km with a 20% level of profitability will amount to $60-80 per TOE. Thus wood chips are noncompetitive as compared to natural gas delivered from Russia at preferential prices that is used as the main type of fuel in the national energy sector. It should be noted that the preferential prices for natural gas are temporary. When Russia and Belarus join the WTO, the natural gas prices will be formed in accordance with the world market prices.
At present, however, to achieve a wide-scale use of wood fuel at power generating facilities will undoubtedly require support from the state.
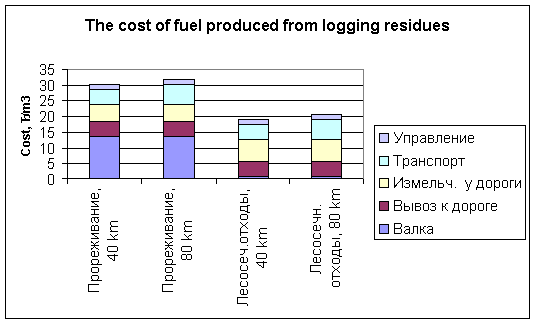
Ïðîðåæèâàíèå 40 êì |
Thinning 40 km |
Ïðîðåæèâàíèå 80 êì |
Thinning 80 km |
Ëåñîñå÷íûå îòõîäû 40 êì |
Logging residues 40 km |
Ëåñîñå÷íûå îòõîäû 80 êì |
Logging residues 80 km |
Óïðàâëåíèå |
Management |
Òðàíñïîðò |
Transport |
Èçìåëü÷åíèå ó äîðîãè |
Comminution at the roadside |
Âûâîç ê äîðîãå |
Transportation to the roadside |
Âàëêà |
Felling |
As in Finland wood fuel is delivered to power generating facilities in large volumes, the calculation of fuel quantity used in the settlements with suppliers is simplified to the maximum. As has been mentioned earlier, the payment is made for the delivered energy units rather than for cubic metres or tons.
When a chip truck with wood fuel arrives at a boiler plant, it is weighed 2 times: before and after the truck is unloaded. The driver collects three 1 litre test samples into special transparent bags and hand them over to the laboratory to determine the moisture content of wood. The moisture content of wood is determined by weighing the test samples preliminarily dried in a drying cabinet. Once a year the chip samples collected at small boiler plants are submitted to specialized laboratories for a more accurate determination of the calorific value using the calorimetric method. Large boiler plants have their own specialized laboratories equipped with calorimeters. The calorimetric method is used to monitor the calorific value on a monthly basis. The moisture content is also monitored on a daily basis by weighing the test samples preliminarily dried in a drying cabinet.
The training course was concluded by conducting practical studies where two groups of participants prepared independently of each other the draft proposals for the production methods and the set of equipment to be used at an enterprise engaged in harvesting, removing, comminuting and transporting logging residues to a boiler plant under the conditions existing in Belarus using the knowledge and experience obtained in the course of training in Finland.
Conclusions
1. As the wood processing waste is usually consumed at the woodworking enterprises where it is produced either in the form of fuel or a raw material, the main source that can be used to increase the production of wood fuel for large power generating facilities are the wood chips produced from logging residues and obtained from sanitary fellings and thinning operations.
2. The full range of machines required to produce wood chips has been designed and is being manufactured in Finland. These machines are being further improved by increasing their reliability, performance, the degree of mechanization and automation so as to decrease the cost of production of wood chips.
3. The cost of wood chips on the Finnish market is currently ˆ10.4 per 1 MWh, which is equivalent to $101.5 per TOE. Despite the minimum level of profitability of production of wood chips, a number of powerful operators act on the Finnish market. Where the cost of harvesting food chips exceeds the market level (thinning operations), the production of wood chips is subsidized by the state.
4. In Finland boiler and cogeneration plants are actively trading in CO2 quotas, which brings them additional profit from the use of wood fuel. The price of a ton of CO2 is ˆ20-22.
5. The Republic of Belarus has a strong industrial potential, which makes it possible to launch the production of new equipment designed to produce and transport wood chips within a short period of time. The least developed production component are mobile chipping machines. The chippers being manufactured in the country have low capacity and are insufficiently reliable.
6. The preliminary estimate shows that the cost of the fuel chips delivered to a boiler plant over the distance of 50 km with a 20% level of profitability will amount to $60-$80 per TOE. Thus wood chips are noncompetitive as compared to natural gas that is delivered from Russia at preferential prices and used as the main type of fuel in the national energy sector. It should be noted that the preferential prices for natural gas are temporary. When Russia and Belarus join the WTO, the natural gas prices will be determined by the world market prices. At present, however, to achieve a wide-scale use of wood fuel at power generating facilities will undoubtedly require support from the state.